- Solution overview
Manufacturing supply chains: Parts management as-a-service
Synchronize data, processes, and people to revamp parts management
The challenge: get a handle on data to upgrade parts planning
Parts manufacturers struggle to keep customers supplied with the parts they need, when they need them. This could stem from a lack of knowledge about the installed base, or because disparate order management, inventory planning, fulfillment, and maintenance systems mean data is frequently out of date or inaccurate.
The upshot? OEM customers face unpredictable lead times and excessive downtime,and their planning and productivity suffers. And, in addition to sliding customer satisfaction, manufacturers face rising costs from excess and obsolete inventory.
Supply chain professionals with the know-how to solve these problems retire,making this even worse.
Our solution: integrate, streamline, and harmonize parts-planning and service
Genpact's parts management as-a-service model integrates order management, buffer stock planning,and demand-based fulfillment into a single system for parts management and fulfillment. All kept on track by reconfigured processes.
We start by building strategic scenarios to help you evaluate business decisions under real-world conditions.These scenarios define, then simulate ideal service levels and fill rates. We consider field capacity, compare trade-offs, conduct a gap analysis, and define all network requirements in detail. When we're done, we help you choose the strategy that best meets your business goals.
Based on this strategy, we build the planning systems and processes to meet your order, fulfillment, and service goals, bolstered by continuous functional application support and fine-tuning. Analytics and automation improve planning and productivity.
Take a copy for yourself
A control tower and orchestration platform coordinates order management, fulfillment, shipping, and field service activities. Data is visible, service levels improve, and collaboration grows.
This as-a-service solution means we are with you every step of the way – from planning to execution – to make sure you get the results you need.
Figure 1: Parts management as-a-service: Modular offerings for planning and execution
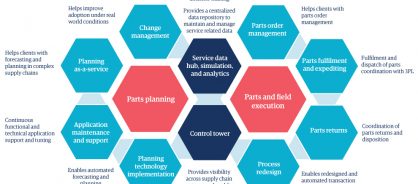
The impact: happier customers– a healthier bottom line
Our parts management as-a-service solution has delivered significant results for our customers. Typical benefits include:
- 50-60% planning and execution productivity gains
- 3-4% increase in operating margin
- 5-10% improvement in on-time, in-full deliveries
- 10-15% reduction in inventory levels
- 25% boost in forecast accuracy
- 70-90% automation of order entries
- 50% shorter order lead time
- 20-30% better expediting efficiency
How an aircraft manufacturer's parts planning took off
Genpact transformed the manufacturer's service-parts planning and replenishment processes by syncing inventory supply and demand in inventory. Benefits included:
- Year one savings of more than $300 million from parts planning and supply chain efficiencies
- Additional savings of more than $250 million each year from improving predictive maintenance using remote monitoring and data analytics
- An annual reduction of 8,000 requests from the fulfillment team
- A 75% boost to its customer notification report success rate