- Solution overview
Consumer goods supply chains: On-time, in-full delivery management
Boost OTIF rates with a 360° view of the supply chain and proactive problem-solving
The challenge: deliver goods when customers want them and avoid hefty fines
Meeting on-time, in-full delivery targets is one of the biggest issues facing consumer packaged goods (CPG) companies today. Retailers are under pressure to reduce costs and shore up margins and they know that late deliveries and stock outs mean lost sales. To stay competitive, some large retailers are insisting that suppliers up their game when it comes to order fulfillment and on-time deliveries, imposing substantial fines for early, late, or incomplete deliveries.
The impact on CPG manufacturers’ revenues and margins can be significant, but they face multiple challenges to meet OTIF targets. Production issues, late pickups, picking errors, stock outs, quality issues, and warehouse problems all negatively impact deliveries to retailers. Transportation issues such as damage in transit and early or late deliveries also l add to the problem.
Take a copy for yourself
Our solution: identify and mitigate the root cause of delivery failures
To make sure CPG companies meet their OTIF targets, understanding and mitigating the cause of delivery failures is mission critical. Genpact's OTIF solution uses predictive analytics, root cause analysis, and real-time visibility to proactively identify, address, and prevent the causes of OTIF failures before they impact customers.
It's an early warning system that identifies upstream events before they become downstream customer problems. For example, if a potential shortage is flagged five days before an order is scheduled to ship, alternative ways to fill the order can be put in place instead of learning about the cut after it's happened.
Here's how the solution works. We make an initial assessment of the upstream factors in supply chain performance such as production and fulfillment processes to identify why OTIF targets are being missed, then use this assessment to recommend an OTIF strategy and roadmap.
Next, we establish an OTIF control tower that sits on top of your existing technology framework and connects to your production, warehousing, and transport systems. This sends alerts based on inventory status, order fulfillment, and expected delivery timelines so that sales, order management, and transport-planning teams can make proactive customer delivery decisions using predictive analytics, root cause analysis, and real-time data. Upstream failures are quickly flagged and acted upon before they impact OTIF targets.
Genpact's Cora Orchestration digitizes, automates, and manages workflows, coordinating multiple teams' activities through one system. This streamlines communications between the CPG company and retailers, reducing the need for emails and phone calls. It tracks orders in real time so that retailers know where their orders are and when they will be delivered.
The system calculates the fastest way to ship inventory and adjusts where goods need to go to match demand. It also modifies orders based on the best sourcing location and arranges alternative carriers if needed, sends alerts to customers, and reschedules deliveries when necessary to prevent the causes of OTIF failures.
Figure 1: A holistic connected dealer and service solution
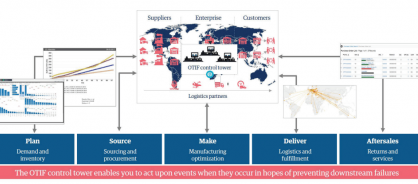
The impact: steep declines in OTIF failure fines. Big boosts to forecasting and productivity
Our OTIF solution improves our customers' forecasting, planning, and transportation usage. Fewer upstream failures means better OTIF performance.
In just 26 weeks, we helped a US food and beverage major cut its OTIF fines in half, saving $5 million in fines by increasing visibility into the events that lead to OTIF fines. By providing near real-time insights into supply chain performance, our OTIF strategy ensures that the company is producing and delivering the right products at the right time.
Overstocking is down, the firm is responding to short orders faster, and its OTIF rate has jumped from 79% to more than 85%.
Genpact Cora Orchestration has also improved resource utilization by up to 19%. Newly standardized processes mean the enterprise can quickly determine the root causes of logjams and move to resolve them before they escalate. And this automation means that workers are spending less time manually collating, preparing, and analyzing data.
- Case study
Struggling to meet on-time, in-full delivery demands?
One of America's largest consumer goods companies needed help meeting on-time, in-full delivery targets. Genpact's solution flags transportation issues before they lead to OTIF failures and has boosted OTIF deliveries to nearly 90%.
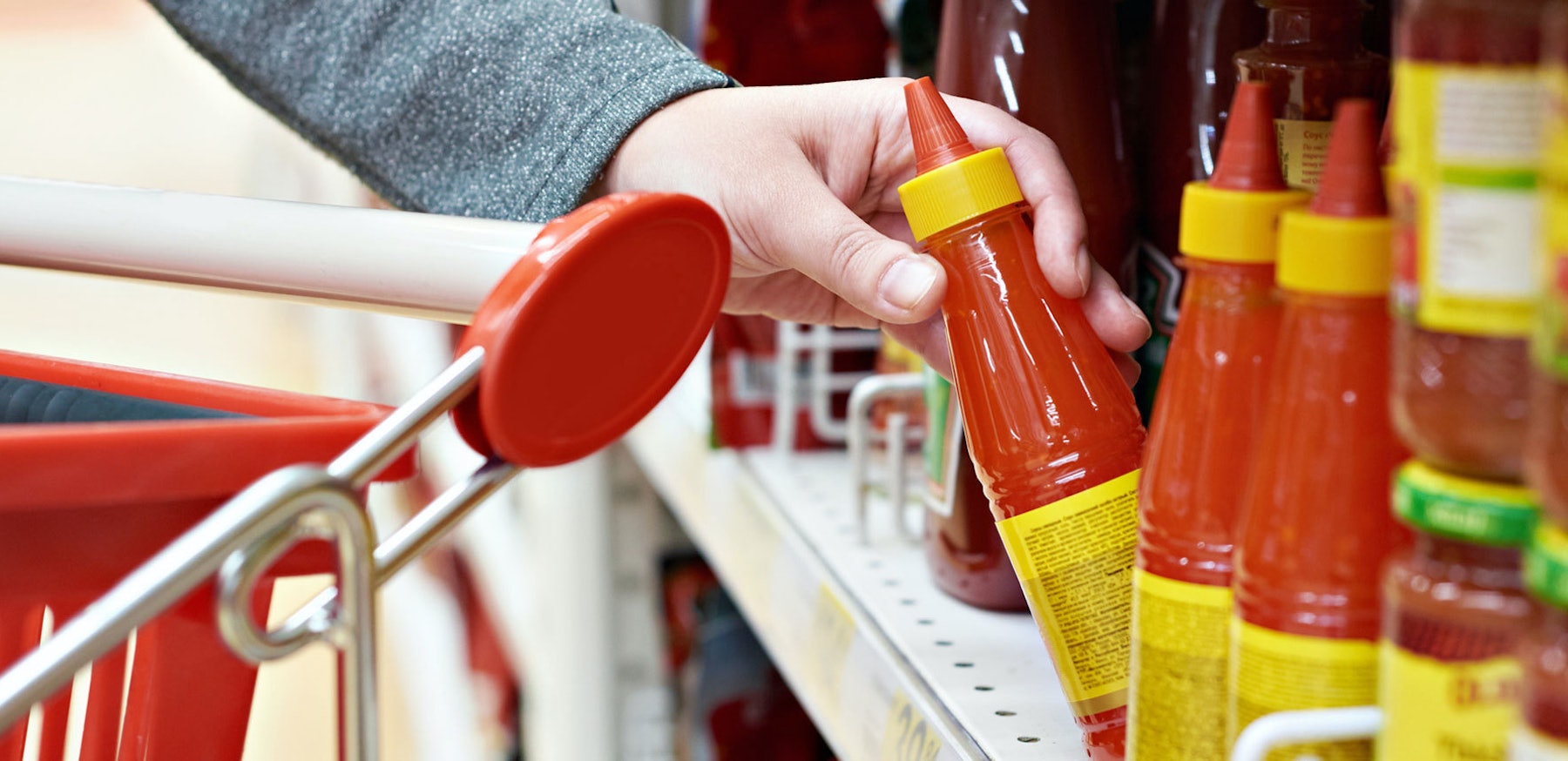